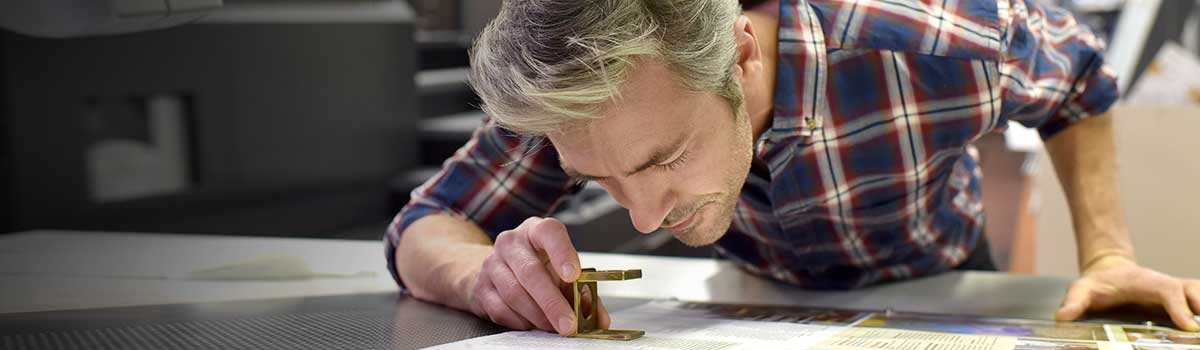
4 Signs You Need to Upgrade Your Print Technology
When you’re running a busy print shop, it’s easy to lose sight of the bigger picture.
You’re so focused on getting work out the door, you don’t have time to ask yourself the big questions: How has the market changed? Am I keeping up or falling behind? How do I stack up against the competition? Does my business model still make sense? Where will I be in a year — or five years?
Often, the answers to these and other questions come down to the technology you’re using. After all, you’re only as productive, efficient and competitive as your press(es). And if you haven’t upgraded in the last few years, you may be missing out on new business, or new opportunities with existing clients.
Here are four signs that it might be time to upgrade your print technology:
1. You’re Selling On Price
In recent years, there’s been a lot of downward price pressure in the print market due to the emergence of online print shops. With their lower costs, larger client bases and faster delivery times, it can be hard for you to compete if you’re doing a lot of labour-intensive, low-value work.
Online print shops’ high-volume, low-margin model means they can usually undercut you on price for this type of work. And it’s not just the online competition. Your local competitors may also be selling on price to retain market share.
You may feel tempted to adopt the same strategy, but competing on price is a race to the bottom – and that’s a race you never want to win. Instead, the answer is to differentiate yourself, offering value-added services that neither online nor offline competitors can match – delivering premium print jobs at premium prices. You could become a valued marketing partner instead of ‘just another print shop’. And upgrading your technology can help you get there.
2. Waste Is Eating Into Your Profit Margins
Even in a perfect world, jobs go wrong. What matters is how often it happens and how seriously it hits your bottom line. A good way to see the size of the problem is to look at the size of your wastebasket.
If you’re using older technology you might think waste is normal. Those alignment, skew and magnification problems are just part of the process. The same goes for colour density issues, which can sometimes force you to throw out a whole job. Paper jams are always frequent when you print on different stock or when humidity increases and paper expands. Paper seldom cuts straight, and blemishes are par for the course.
But this isn’t normal. All of this waste adds up and can seriously eat into your profit margin. It’s not just the cost of the materials – it’s also the drop in productivity, the opportunity cost of lost jobs, and the hit your reputation takes as lead times are extended and deadlines missed.
Newer presses automate and simplify the processes that cause a lot of this waste. Automatic front-to-back registration, stock profiles that control paper temperature and auto sheet clearing (to un-jam your press without you hardly lifting a finger) are just some of the advances that make sure you keep waste levels low and productivity levels high.
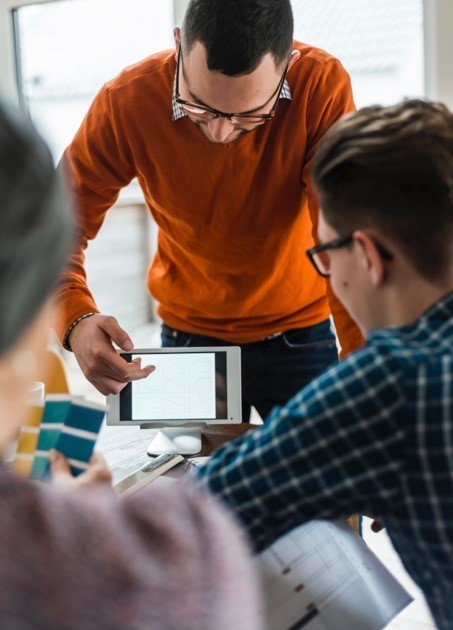
3. You’re Turning Away Work You Could Do
In the end, profitability and success come down to one thing: how fast you can get the work out. And your throughput is dictated by the limits of your technology.
Turning away work you know you could do — if only you had more hours in a day — is probably something you’re familiar with. But what choice do you have?
Print jobs take a long time to set up — especially complicated ones. Even repeat jobs sometimes take as long as the original, since all the parameters need to be re-entered. Heavier stock means running your press at lower speeds, which hits your productivity. The point is, you simply can’t get the work through fast enough to handle increased volumes and still meet client deadlines.
Or can you? With new print technology, quicker job setup and saved workflows make repeat print runs easier than ever. Speeds of 100ppm on stocks up to 350gsm and mixed media jobs means you’re getting the work out at a rapid pace.
4. You’re Turning Away Work You Can’t Do
Adding value isn’t just at the top of your mind. It’s probably at the top of your customers’ wish list as well. Their expectations have been raised by an online world with endless choices, and they may increasingly be asking for things you can’t deliver.
Higher expectations mean more complexity. Perhaps they’re asking for new substrates like plastic/polyester, textile (such as linen or non-woven fabric), foil or promotional magnets. Or maybe they want complex jobs with elements (foldouts, graphics, tabbed dividers, different stocks, special folds, advanced finishes) that are beyond the capability of your press to produce automatically.
So you’re faced with a difficult choice: turn these jobs away, or take them on and watch your labour costs skyrocket and productivity drop as you resort to manual processes.
Older presses simply can’t handle these lucrative, high-value print runs easily and efficiently. Which is frustrating, because you know there’s more money — and customer retention — to be had in this work.
The Time to Upgrade Is Now
As you can already see, there are plenty of great reasons to upgrade. If you haven’t already done so — either because you’re too busy or you think it’s going to cost too much — you may be missing out.
Technology has advanced faster than most print pros realise, and it costs a lot less than you think. Premium features now come standard even on entry-level presses. Plus, higher productivity and increased throughput mean the time-to-ROI is significantly shorter than with an older press.
So if you’re running a busy print shop and haven’t had the time to ask a few big questions lately, maybe now is the time. Time to come up for air and take a look at what new possibilities await.
Related Articles
Spectrum Print Plus – The Business of Colour, Clients, and Commitment - Xerox
“After months of rigorous evaluation, the clear winner had been right in front of us all along—it was the Iridesse!”
Virtual Designer Training: Xerox Adaptive CMYK+ Kit
Use popular digital embellishment techniques in your designs with adaptive CMYK+ kits on the Xerox Versant and Xerox PrimeLink Production Press
Combatting the Top five Production Operation Cost Drivers
Discover effective strategies to combat the top five production operation cost drivers in digital printing. Learn how to optimise your production processes and reduce costs with expert insights from Xerox.
Unlocking Profits with Digital Embellishments
Get ready to dazzle your clients and boost your bottom line with this power training session from Xerox and Taktiful. Learn strategies to become more profitable marketing, pricing and selling Beyond CMYK applications.
40 Years Strong: Pronto Reproductions and Xerox Forge a Resilient Partnership in a Shifting Market
See how the partnership between Pronto Reproductions and Xerox continues to drive agility and growth in a shifting market with the Xerox® Iridesse® Production Press.
UK printer delivers high-value projects while lowering environmental impact
Rapidity gains efficiency, versatility with Xerox® Iridesse® Presses